Муда, мура, андон и другие совсем не ругательные, а вовсе даже приличные иностранные слова, ошибочно кажущиеся такими знакомыми для русского уха... Если мы не лингвисты, то зачем они нам? Бизнес-тренеры уверяют – нужны! И производственные компании с ними согласны. Далеко не первый год первые лица корпораций учат, что же такое 5S, TPM и даже пока-йока. А теперь и ритейл начал вникать в эти дебри. Посмотрим на них поближе.
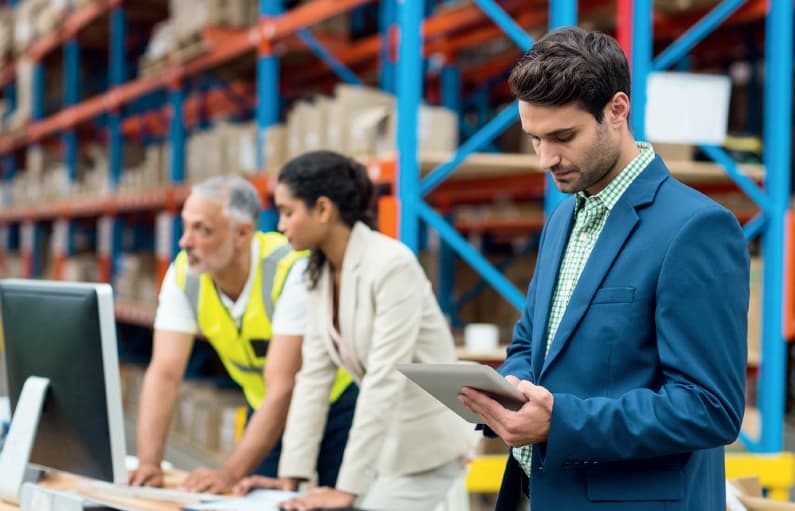
Все термины, которые мы только что перечислили, принадлежат системе Lean. Сама система Lean выросла из принципов работы японской компании Toyota. Абсолютно все, кто говорит про Lean или пишет про систему книги, начинает с этого: «Жила-была Toyota и жила она в стране, у которой почти не было природных ресурсов, да еще там только что завершилась Вторая мировая война; и все было бы плохо, но тут Toyota собралась и придумала, как ей жить и работать дальше, причем жить хорошо, а работать еще лучше».
Так появилась TPS, или Toyota Production System. На нее посмотрели американцы, пересказали у себя, назвали систему Lean. Но подождите, давайте вернемся обратно! И японцы не все сами придумали, они сначала посмотрели, что делают американцы и даже русские. И только тогда уже придумали. В общем, первые несколько страниц всех книг посвящены этой исторической кутерьме и связям в духе «Авраам родил Исаака, Исаак родил Иакова».
После выяснений, кто кого родил, идут объяснения терминов. Встречаются такие логические построения, как «муда первого рода, муда второго рода и муда происходит вследствие муры». В общем, любой русскоязычный человек подтвердит, что в жизни именно так и бывает. Однако к пониманию сути системы его это не приблизит.
Все, больше ни одного непонятного термина всуе мы не употребим. На самом деле речь идет об очень простой вещи. Вы наверняка встречали практические советы для повседневной жизни, которые особенно ловкие товарищи объединяют в систему и начинают проповедовать, издавая красивые книги с картинками. Советы в духе «нет места в шкафу – выкинь то, что тебе мало»; «все равно места не хватает – сверни все футболки рулончиками»; «хочешь быстро находить ансамбли – разложи всю одежду по цветам»; «часто пользуешься – положи ближе»; «летом засунь свитера подальше». Рекомендации очевидные, не правда ли? Но посмотрите в свой шкаф. Там все разложено по цветам и сезонам? Или там куча, засунутая кое-как и грозящая обвалиться в любой момент, когда вы тянете на себя футболку из самого дальнего угла (и она там не в рулончик свернута, ой не в рулончик!).
Примерно такие же советы есть по вопросам организации труда и общего функционирования компании. Если их собрать в систему, то может получиться разное. В СССР возникла НОТ – научная организация труда. В США – Lean, или «бережливое производство». В Японии – TPS. Названия разные, а цель одна: улучшить рабочие места, рационализировать труд и правильно подготовить сотрудников к работе.
Про научную организацию труда у нас забыли, и, я думаю, нет нужды говорить, почему. Зато стали постепенно смотреть на запад и восток – а как у них? И перенимать методы. Сейчас не особенно разделяют системы TPS и Lean. Наоборот, Lean как система вобрала в себя все принципы и термины, поэтому дальше мы будем говорить только про нее.
За что нам платят?
В чем суть? В том, чтобы найти ресурсы к улучшению не снаружи, а внутри компании. Не покупать новые инструменты, не внедрять новые ИТ-системы, не раздувать штат, а найти внутри течь, дыру, через которые убегают деньги и силы, и тем самым сберечь и то и другое – отсюда термин «бережливое производство». В Lean этот процесс называется поиском потерь.
Для начала компания определяет для себя, что именно в ее деятельности составляет ценность для клиента, за что он готов ей платить, а что – просто побочный результат этой деятельности. Это лучше всего объяснять на каком-нибудь примере. Допустим, пассажир сел в такси и едет. Это для него – ценность, он именно за это и платит, за каждую минуту, проведенную в чужом автомобиле. Но вот посреди поездки таксист заехал на заправку, потому что кончился бензин. Пассажир ждет 15 минут. Он сидит все в той же машине, но ценность в это время для него полностью улетучилась. Хочет ли он оплатить таксисту эти 15 минут? Наоборот. Вот этот участок пути и есть потеря в обслуживании. Это очень наглядный пример. В корпорации же такие потери можно выискивать, находить потери неочевидные, вылавливать их по одной, как блох, и так до бесконечности. Отсюда вытекает следующий принцип Lean – непрерывные улучшения. Причем в этом процессе должны участвовать абсолютно все, кто работает в компании, и так всю жизнь. Lean – как зарядка по утрам. Нельзя сделать один раз в год и на этом успокоиться.
В системе еще много самых разных принципов. Например, ориентация на потребителя, гибкость, «вытягивающее производство» (когда говорят «нет» огромным запасам на складах, незавершенному производству, и «да» – работе под проект, под заказ, по надобности и по запросу отдела, чтобы ни одной ниточки даром не произвести и не выкинуть без пользы), определенный порядок на рабочем месте, визуализация, когда все подписано, отделено друг от друга, наглядно, когда картинки такие, что работник, глядя на них, не может ошибиться и что-то перепутать.
О таких подробностях лучше читать книги, потому что каждый принцип там разжеван и проиллюстрирован примерами из практики. Мы же лучше задумаемся вот о чем. Система выглядит разумно и здорово. Более того, она настолько соответствует здравому смыслу, что, узнавая о ее принципах, мы даже можем воскликнуть: о, так я примерно так и хотел сделать у себя! И самое приятное: неважно, где это «у себя». Lean как методология возникла на производстве, но оказалась применима к самым разным рабочим сферам: ее внедряют даже в больницах! «Ни у одной из методологий практически нет жестко зафиксированной области применения: SCRUM применяется для обучения детей в школе, а с помощью Lean повышается качество приема звонков колл-центра. Но на то, чтобы бизнес стал получать реальную ценность от кайдзена или холократии, уходит много ресурсов: ведь потребуются значительные изменения в принципах работы, образе мышления», – говорит Денис Напалков, бизнес-архитектор службы организационного развития компании ICL Services.
Ритейл не стал отставать от других и тоже обратил внимание на методологию. «Есть поветрия, а есть вещи долгосрочные, которые уже пережили не один десяток лет, и Lean Production – как раз такая вещь, – размышляет Евгений Рачков, директор консалтинговой группы Lean Consult. – Реально работающих концептуальных методик сейчас по большому счету всего три: это «Бережливое производство», «Шесть Сигм» и «Теория ограничений систем» Элияху Голдратта. Остальные живут от пяти до 15 лет: они приходят, ими увлекаются, на них зарабатывают, и они потихоньку растворяются. В то время как серьезные западные компании, даже среднего масштаба, но с западным мышлением, работают по принципам Lean. В США примерно 60% компаний внедряют у себя методологию. В Японии – около 30%. В России же сложно сказать, но боюсь, что это всего несколько процентов, больше не наберем».
«Пока в российской среде мало успешных кейсов, – соглашается Денис Тверской, руководитель направления «Дистанционное обучение» компании «Топ Менеджмент Консалт». – Хотя в производственном секторе Lean внедряется почти 20 лет, а в секторе сервиса/услуг – более 12 лет».
Если во всем мире так, почему же у нас не хотят последовать вполне разумной методологии? С одной стороны, вполне хотят. Так, разные производители внедряют у себя систему на производстве. Пивоваренная компания «Балтика» не только пытается работать по принципам Lean, но даже показывает результат другим организациям, периодически проводя на территории заводов экскурсии, в ходе которых желающие могут увидеть, как действует Lean на практике.
В основном принципы и инструменты Lean в компании «Балтика» внедряются в цепочке поставок: производстве и логистике. «В распоряжении данной концепции есть богатый инструментарий, который помогает разложить любой рутинный процесс на «молекулы», выявить тренды, закономерности, определить, как этот процесс должен быть организован в идеале и какие неэффективности присутствуют в каждом конкретном случае», – рассказывает Иван Комаров, начальник отдела по повышению эффективности бизнес-процессов функции производства региона Восточная Европа пивоваренной компании «Балтика», части Carlsberg Group. По его словам, данная система включает в себя несколько основ, например, соответствие базовым принципам и стандартам компании, лидерство и организационный дизайн. В дополнение к этому существуют отдельные направления, каждое из которых нацелено на решение целого ряда задач: внедрить культуру безопасности и качества в компании, развить автономное техническое обслуживание оборудования, научиться видеть все потери и уметь устранять их, а также выстроить систему обучения и развития сотрудников, которая отвечает вызовам рынка и необходимым для этого навыкам и компетенциям.
Если говорить о ритейле, то здесь не остались в стороне самые крупные игроки рынка. «Практика Lean внедрена во всех странах присутствия Auchan Retail. В России она действует во всех форматах магазинов, – говорит Игорь Кривошеев, директор по проектам «Ашан Ритейл Россия». – Команда внедрения уже обучила более 1000 сотрудников магазинов основам Lean-менеджмента, благодаря которым они научились смотреть на свою работу через призму постоянного совершенствования. В рамках этого проекта были разработаны и внедрены стандарты, улучшающие работу магазинов в трех направлениях: менеджмент, организация и процессы. Внедрение Lean для деятельности сервисных служб (back-office) запускается в этом году».
Однако это всего несколько примеров. Количество проектов с Lean в ритейле можно пересчитать по пальцам одной руки.
Не винтики, а люди
Вернемся к первоначальному вопросу. Теория есть, и она работает на практике, только не у нас. В ходе Российской недели ритейла этим летом была проведена целая секция, посвященная Lean, но называлась она примечательно: «Бережливый ритейл – недооцененный в России тренд». Что является основной причиной такого невнимания? «Когда я десять лет начинал консультировать компании по методологии Lean, то полагал, что основные проблемы будут с нижним звеном, думал, что новые идеи работники будут саботировать, потому что они недостаточно образованные, «темные». Ничего подобного! Часто самые «темные» и негибкие товарищи находятся наверху», – констатирует Евгений Рачков.
«Lean management – это не только методология, но и образ мышления, – подчеркивает Игорь Кривошеев. – Изменить образ мышления за 6–10 недель внедрения невозможно, эта работа должна быть постоянной и регулярно рекламируемой, в первую очередь высшим руководством с применением действенных мотивационных инструментов».
У кого бы мы ни спрашивали, что нужно для внедрения, все эксперты говорили в один голос – только политическая воля руководства. «Основная проблема освоения Lean для любой компании, будь то ритейлер или производитель, такой как «Балтика», это приверженность руководства принципам этой концепции, – замечает Иван Комаров. – Руководство компании должно понимать фундаментальность этих постулатов. С самого начала важно заручиться поддержкой топ-менеджмента, первые люди компании должны всячески подчеркивать и распространять принципы Lean в своих посланиях и в корпоративной рутине, только тогда концепция начнет работать. Увлеченность Lean может быстро смениться разочарованием, потому что данная концепция не дает быстрых результатов, чего все обычно ждут. Руководители должны обладать определенной мудростью, чтобы не отказаться от заявленных принципов, когда увидят, что результаты появятся далеко не сразу».
Считается, что Lean у нас не приживается, потому что у нас не такие работники, не такая «почва» для нововедений и вообще все не такое, как в Японии (логично!). Полагают, что нам мешает российский менталитет. «У нас любят говорить, что нашим «танцорам» менталитет мешает. У меня есть на это возражение, – замечает Сергей Смирнов, генеральный директор Национального центра производительности. – На российский рынок с нашим якобы особым российским менталитетом приходят западные компании и спокойно строят тут компании, которые становятся вполне конкурентноспособными, с качественным продуктом».
Если мы посмотрим на историю Lean, то увидим: нигде не было легко внедрять новую методологию. Когда Ацуси Ниими, бывший президент Toyota, в Северной Америке обучал американских управленцев, то заметил, что самое трудное в этом деле было изменить их мышление. «Они хотели руководить, а не учить», – говорил он, в то время как в Toyota в Японии утверждали: «В первую очередь мы делаем не машины, а людей».
Если рыба гниет с головы, то вполне естественно предположить, что и оздоровление она должна начинать тоже с головы. «Если руководитель не разделяет ценности бережливого производства, если в его картине мира люди – это винтики, то ничего не выйдет в принципе, – уверен Евгений Рачков. – Вся бизнес-система должна самообучаться: от верхнего звена к нижнему. Все люди должны участвовать и думать. А винтики не думают, винтики исполняют свою маленькую роль».
Ищем выгоду для всех
У Lean есть как минимум несколько уровней реализации. Первый уровень – это та самая политическая воля руководителя. Именно руководитель задается вопросами о том, как сделать бизнес эффективнее; можно ли добиться улучшения показателей без дополнительных инвестиций в оборудование. Второй уровень – это межфункциональное взаимодействие. Об этом рассказывает Сергей Смирнов: «Внедрение Lean – это не проект отдельного подразделения, а проект всей команды в компании. Ведь у нас как бывает? Руководство решило внедрять, назначило пилотный участок и давай наводить там порядок. А вся остальная система работает так же, как и раньше, и смотрит на этих чудаков с неодобрением: мол, какие улучшения, тут работать надо, план горит! А ведь потери можно найти абсолютно во всех отделах, даже в каком-нибудь далеком HR-отделе, хотя они, казалось бы, ничего не производят и с покупателями не общаются. Но на каждом этапе по рекрутингу, по найму, по оформлению документов мы легко найдем кучу потерь. Если мы посмотрим на службу, которая отвечает за работу оборудования, то увидим, что потери и место для непрерывного улучшения есть и там».
Третий уровень – вовлечение всех сотрудников. Они должны четко увидеть, что получат лично они на своих рабочих местах, и должны понять, почему им стоит участвовать в проекте под названием Lean. «Многие работники говорят: «Не надо нас мотивировать. Прекратите демотивировать», – делится наблюдениями Сергей Смирнов. – Ведь тут есть один тонкий момент. Вот внесли они рационализаторское предложение, реально что-то улучшили и начали работать. Что происходит дальше? Знаете? А я вам скажу. Через три недели приходит нормировщик и пересматривает им нормы. Я спрашиваю: коллеги, а если вам вот так нормы пересмотрят, вы лично будете еще раз подавать рацпредложение? Или лучше будете сидеть тихо? Вы хотите получить экономическую прибыль, платя меньшие зарплаты? Или мы о другом все-таки говорим? Ведь на этом этапе можно легко обрубить любую творческую деятельность на местах».
Тише едешь – дальше будешь
Очевидно, что Lean дает хорошие результаты при высоком вовлечении топ-менеджмента компании, и при этом ей нужно время. «Мы пока еще не научились думать стратегически на несколько лет вперед, – объясняет Денис Тверской. – Новые возможности, которые нам открываются благодаря техническому прогрессу, заставляют думать о прибыли, которую можно получить прямо сейчас или хотя бы в ближайшем будущем. На бизнес влияет боязнь перемен, связанных с политикой, ситуацией и взаимоотношениями с другими странами. Мы боимся вкладывать капитал в развитие компании и повышение дохода в относительно рискованном будущем, если есть альтернатива получения прибыли быстро».
Как долго придется ждать? ««Когда мы говорим про культуру, мышление, то нужно понимать – это вещи очень инертные. Когда я внедрял систему «бережливого производства» в своих компаниях, то видел возникновение четких, устойчивых моделей поведения через полтора-два года, и это при учете того, что занимался этим последовательно и регулярно», – рассуждает Евгений Рачков.
В компании «Балтика» концепция Lean стала активно внедряться в производственную цепочку с 2012 года. Прошло почти семь лет. «За то время, пока мы внедряем бережливое производство, в компании произошли настоящие ментальные изменения. Даже непрофессионалы могут видеть различия между предприятием, которое на практике применяет концепцию бережливого производства, и тем, которое только декларирует ее внедрение, – воодушевлен Иван Комаров. – Теперь мы можем говорить о существенном развитии культуры безопасности и системы качества, росте производительности труда и надежности работы оборудования. Внедрение Lean позволило улучшить эргономику рабочих мест, снизить количество поломок, неисправностей и технических простоев на оборудовании, что влечет за собой сокращение издержек и рост производительности труда. Сама по себе Lean не дает результат моментально, и если вся компания привержена ее принципам, то первые плоды начинают появляться через несколько лет. Изменения в рабочих процессах «Балтики», связанные с внедрением Lean, сейчас заложены в «ДНК» компании, а такие вещи не происходят по щелчку пальцев».
«Российский бизнес привык мерить все дисконтными мерками, а в философии Lean надо мыслить тактически, – добавляет Антон Мартьянов, директор по цифровой трансформации, группа компаний D.O.L.G. – Кто будет первым, тот получит некое неожиданное для рынка конкурентное преимущество и вырвется в лидеры».
Учись, мой сын
Один из краеугольных камней Lean – это обучение сотрудников прямо на производстве (TWI, или Training Within Industry). «Программы TWI значительно повлияли на развитие концепции Lean. TWI можно назвать корнями Lean, хотя и не единственными, потому что отличительные черты бережливого производства сформировались под воздействием многих факторов. Применение TWI помогает в решении части проблем. Например, оно полезно в области обучения людей, совершенствования технологии работы, создания среды постоянных улучшений», – говорит Денис Напалков.
Обучение на производстве противостоит такому явлению, как «кривая жизнеспособности». Ее проводником в жизнь был американский бизнесмен Джек Уэлч, который помимо прочего 20 лет управлял компанией General Motors в качестве генерального директора. С одной стороны, ему принадлежат цитаты вроде «пока ты не лидер, твой успех в том, чтобы развивать себя; когда ты становишься лидером, твой успех в том, чтобы развивать других». С другой – господин Уэлч подсчитал, что в любой организации есть 10% «паршивых овец», от которых надо немедленно избавляться. Звучит в общем-то разумно. Но Джек Уэлч избавлялся от этих процентов каждый год, выискивая все новые 10% в уже просеянном коллективе. Компании, которые пытались действовать так же (некоторые до сих пор пытаются), довольно быстро обнаруживали все минусы подобного подхода. Джека Уэлча назвали «управленцем №1» по версии журнала Future, в то время как в народе его звали «нейтронным Джеком», сравнивая этот стиль управления с нейтронной бомбой, которая уничтожает все живое, а здания оставляет целыми. Но Уэлч не особенно волновался по поводу чьих-то там мнений. «Вы становитесь управленцем не для того, чтобы всем нравиться, а для того, чтобы управлять», – говорил он.
«За любым инцидентом на предприятии стоят навыки сотрудников, а точнее, их отсутствие. Но сотрудников нужно обучать, а не выкидывать за борт. А если ученик не научился, значит, инструктор не научил. Дело в том, что если я как инструктор соблюдаю стандарт обучения, а ученик достаточно мотивирован, то он не может не усвоить тот или иной навык. Бывает, что люди сомневаются, говорят, что бывают вообще необучаемые. Я им отвечаю – не бывает! Это вы не доработали, – восклицает Сергей Смирнов. – При этом я считаю, что нет и таких, которые не предрасположены к обучению других. Все люди могут обучать».
Lean Production – это прежде всего изменение культуры мышления и поведения. Чтобы достичь этого изменения, нужно заложить базу, подготовить почву, в том числе и с помощью TWI. «Но, наверное, вы и сами знаете, насколько в России «любят» инвестировать в персонал, – смеется Евгений Рачков. – Все боятся инвестировать в работника, который может убежать на сторону сразу после того, как компания в него вложится. Многие руководители считают, что в оборудование или даже в софт вкладываться надежнее – у них ног нет. Это основное препятствие для руководителя в данном вопросе, потому что вложиться в персонал – это вообще-то недешево».
По словам Сергея Смирнова, обучать сотрудников на производстве стоит даже тем ритейлерам, которые боятся вкладываться в обучение из-за текучки кадров. «Мы реализовывали у одного ритейлера программу TWI. Это основа, то, из чего выросла система Lean. Наша программа была направлена на анализ и развитие трудовых навыков сотрудников, потому что показатели компании, допустим, по количеству претензий от покупателей, являются вполне объективным критерием уровня подготовленности его работников. В рамках программы мы обучили директоров, те, в свою очередь, обучили продавцов и кассиров, и буквально на следующий день у них растет средний чек, повышается оценка лояльности клиентов (по сведениям от «тайных покупателей»). Если ритейлу страшно вкладываться в сотрудников из-за текучки, то пусть посмотрят на компанию McDonlald’s: громаднейшая сеть, 32 тыс. ресторанов по всему миру. И у них с текучкой кадров ситуация не лучше, чем у других: порядка 30%, и это все признают. При этом задача бизнеса – обеспечивать высокое качество обслуживания клиентов в своем сегменте. И заметьте, они приходят в любую страну, с любым менталитетом и с любыми сотрудниками, а качество обеспечивают по стандарту. Потому что у них есть методы, которые обеспечивают быстрый и качественный ввод любого специалиста в дело. Через четыре – восемь часов сотрудник стоит и выполняет свои обязанности так, как положено».
А вот отзыв от фабрики «Большевик», чьи сотрудники прошли такое обучение. Рассказывает Дмитрий Шаченок, директор: «Я считаю, что мы научили людей обучать других. Это наш главный результат, что теперь, когда мы начали внедрять бережливое производство, становится особенно очевидно. Мы создали базу, поэтому традиционного шока, какой бывает от внедрения Lean, у нас не произошло».
TWI – это недостающее звено в системе бережливого производства. Во многих компаниях без TWI-программы просто не начинают вводить Lean, потому что не сработает. «Обучение Lean в чистом виде действительно даст слабый эффект, – говорит Денис Тверской. – Приведу пример, но не буду называть бренд, однако поверьте: он знаком большинству читателей. Компания с 2013 года пытается внедрить Lean. Взяли в штат достаточно успешного руководителя на высокую должность. Но у него не было практического опыта применения Lean, хотя теорию он знал на отлично. А средний менеджмент не владел управленческими навыками, но в своем сегменте они были отличными специалистами. К чему все это привело? Взятый на руководящий пост директор по Lean не смог донести важность и пользу этой технологии до всех руководителей среднего звена. А те, кто понял, уже не смогли распространить эти знания и воплотить в жизнь на своем уровне. Результатом стали только красивые картинки и листы аудитов двухмесячной давности. А ведь за все это компания заплатила немалые деньги».
Поле боя
Очень важно помнить, что методология – это не то же самое, что инструмент. Это не молоток, который либо забивает гвозди, либо лежит на полке. Для успешного освоения Lean в любой компании должно быть глубокое понимание методологии и сфер ее применения внутри организации. «Часто в компаниях внедряются отдельные инструменты Lean, которые без создания культуры постоянного улучшения либо не дают результатов совсем, либо имеют краткосрочный эффект», – делится опытом Игорь Кривошеев.
Есть у нас и еще одна проблема, которая мешает эффективному применению системы на практике. «В России есть особенность: мы нация, ориентированная на технику. Не на технологию, а именно на технику, обратите внимание! Мы можем подковать блоху, но не можем сделать технологию подковки блох, – рассуждает Евгений Рачков. – И поскольку мы нация техническая, то мы очень сильно любим всякие инструменты. Большинство запросов от бизнеса такие: «Дайте нам инструменты!» А в «бережливом производстве» суть не в инструментах. Инструменты, конечно, нужны и их достаточно много. Но главное в этой системе, на мой взгляд, – это сформировать культуру и мышление самоорганизующейся, самообучающейся и саморазвивающейся организации. И сделать это гораздо сложнее, чем просто освоить набор инструментов».
Когда говорят Lean или «бережливое производство», то, особенно у русскоговорящих, могут сложиться неверные представления: «Под словом Lean нужно понимать гораздо больше. Вводят понятие «производственная система», но из-за привычного звучания у незнающих складывается ощущение, что речь идет только о производстве. Поэтому лично я предпочитаю выражение «операционная эффективность», – объясняет Денис Тверской.
Lean – самый эффективный способ для снижения себестоимости продукции или услуги. По той причине, что именно эта методология позволяет очень оперативно реагировать на изменение рынка. Об этом говорит Денис Тверской: «Возьмем компанию Zara, которая является, безусловно, лидером в своем сегменте. А сегмент этот, как мы знаем, очень изменчив, ведь вещь, которая была в тренде, и ее покупали месяц назад, сегодня уже никому не нужна. Находясь в секторе масс-маркета, сложно работать «под заказ», так как время здесь крайне важно: не успел вывести новую коллекцию, клиенты пойдут и купят похожую модель у конкурентов, а когда она окажется у нас на прилавке, не будет никому нужна. Поэтому у компании Zara очень грамотно и правильно построена система обратной связи с клиентами, которая помогает быстро реагировать на изменение рынка. Под эту же систему построена и поделена на этапы потоковая система производства».
Чтобы не сложилось ощущения, что система неприменима нигде, кроме заводов, мы спросили у представителей компании «Ашан», каким образом именно продуктовый ритейл может применить у себя Lean? Не слишком ли это сложно на практике? Отвечает Игорь Кривошеев: «В современном ритейле есть собственное производство, логистика, клиентский сервис, e-commerce, взаимодействие с поставщиками, ИТ, а еще вдобавок ко всему неэффективно выстроенные процессы в back-office. Со всеми техническими заданиями процессов ритейл – это короткие повторяющиеся циклы со своими измеримыми показателями эффективности и со своей ценой. При этом работа над улучшениями в каждом из названных элементов не требует каких-то особенных знаний, которых нет внутри компании. Исходя из этих пунктов мы уже видим, что ритейл – это отличное поле применения Lean».
Краткий словарь некоторых терминов Lean
Поток создания ценности – все действия, как создающие ценность, так и не создающие ее: от разработки концепции продукта до запуска в производство и от принятия заказа до доставки, а также обработка информации, полученной от клиента, и операции по преобразованию продукта по мере его продвижения к клиенту.
Потери – любое действие, которое потребляет ресурсы, но не создает ценности для клиента.
Анализ узких мест – определение этапа производственного процесса, который снижает общую производительность, и проведение улучшений на этом этапе.
Система 5С – принципы организации рабочих мест с целью устранения потерь и стандартизации рабочих мест путем наведения порядка, поддержания чистоты на рабочих местах и соблюдения дисциплины персоналом.
Кайдзен – непрерывное улучшение. Японская практика, которая фокусируется на непрерывном совершенствовании процессов производства, разработки, вспомогательных бизнес-процессов и управления, а также всех аспектов жизни.
Канбан – визуализация рабочего процесса с помощью карточек. Карты нужны, чтобы команда всегда понимала, какие задачи могут подождать, а над какими необходимо работать прямо сейчас.
Пока-йока – защита от ошибок. Сотрудники не должны замалчивать и скрывать ошибки, дефекты, не должны относиться к ним как к нормальному явлению. Чем скорее обнаружится брак, дефект или ошибка – тем лучше для всех.
Виды потерь в системе Lean
• Ожидание
• Транспортировка
• Перемещения
• Перепроизводство
• Излишние запасы
• Излишняя обработка
• Дефекты
• Нереализованный потенциал сотрудников
Несколько факторов успеха для внедрения Lean (по версии компании «Ашан»)
1. Поддержка руководства. Внедрение Lean-мышления начинается с руководства компании. Это должно выражаться в целеполагании, управлении командой, ежедневных коммуникациях и демонстрации умения ее использования.
2. Мотивация внутренняя. Сотрудники должны понимать, зачем они это делают, и внутренне принять принцип постоянного улучшения. Для этого команда внедрения проводит замеры основных KPI деятельности до внедрения Lean и после. Как правило, положительный результат производит очень сильное впечатление на сотрудников магазина, и это дает первичный «заряд» для дальнейших действий в этом направлении.
3. Мотивация финансовая. Качество работы по Lean можно измерить. Пример: количество жалоб от клиентов, объем списаний в рублях, OOS (Out of stock), размер стока и т.д. Ежеквартальные улучшения по всем этим показателям должны быть непосредственно связаны с бонусной системой, ведь финансовая составляющая всегда была и будет мощным инструментом мотивации.
Практика магазинов «Ашан»
Внедрение Lean продиктовало следующие изменения на местах:
• Внедрены визуальные инструменты. Например, созданы информационные стенды для сотрудников в рабочей зоне магазина. Такие инструменты позволили оптимизировать нагрузку на сотрудников магазина, сопоставить графики, наладить коммуникацию между сменами, сделать доступными KPI деятельности магазина, осуществить краткосрочное планирование. За счет визуализации деятельность магазина становится прозрачной, и именно это является базой для определения областей, которые нуждаются в улучшении силами самих сотрудников каждого конкретного магазина.
• Проведена стандартизация процессов заказа, выкладки, списания, работы с промо и отсутствием товара на полке. Это позволяет магазинам обмениваться лучшими идеями и быть уверенными, что они применимы.
• Введена 5S (система организации рабочего пространства). Например, устроены выкатные ящики под полками, где хранятся инструменты, которыми ежедневно пользуются сотрудники торгового зала. Отведены места для хранения стремянок. Удобнее организована работа с палетами и штучным товаром на складах магазинов. Проделано множество подобных улучшений, и улучшения продолжают ежедневно внедряться сотрудниками магазинов, – все это без участия центрального офиса и привлечения сторонних консультантов.
Риски при внедрении Lean (по версии компании «Балтика»)
1. Нельзя становиться на неправильный путь, когда под видом Lean происходит просто сокращение операционных издержек без изменения бизнес-процессов. Происходит дискредитация бережливого производства, и наступает разочарование в этой концепции, персонал видит в ней лишь массовые сокращения.
2. Необходимо формирование стратегии внедрения, а не точечное использование Lean.
3. Нужно терпение, понимание того, что результат придет не быстро. Если сегодня мы закладываем фундамент, то плоды применения Lean сможем видеть только через несколько лет. Поэтому очень важно заложить этот фундамент в успешные для компании времена, когда на это есть ресурсы, а не во времена спада, когда руководство начинает задумываться о повышении эффективности и экономии.
Риски при внедрении Lean (по версии компании «Топ Менеджмент Консалт»)
1. Обучение персонала происходит ради флага с надписью «Мы внедряем Lean». Такая практика никогда не даст результата, вместо эффекта мы получим демотивацию персонала и неправильное понимание самой сути Lean.
2. Быстрое необдуманное применение всего подряд. В глазах инициаторов это может выглядеть блицкригом, тогда как в глазах персонала и компании – очередной безумной идеей руководства.
3. Ориентация на теорию/теоретика. Метод проб и ошибок можно рассматривать как альтернативу, но в ритейле, где своя специфика и высокие скорости реакции на клиента, такой подход губителен. Самое здравое решение – внедрение вместе с практиками, знающими рынок, среду и специфику.